高精度连接器(如医疗设备、汽车高压、5G 通信领域)必须采用注射成型(LIM),核心在于其对微米级精度、材料一致性、生产稳定性的极致要求,模压工艺无法满足以下关键需求:
-
材料流动均匀性
- 注射成型:液态硅胶(LSR)通过热流道系统(温度波动≤±1℃)以恒定压力(20 - 50MPa)注入模具,粘度低(1000 - 10000mPa?s)且流动平稳,可填充 0.1mm 以下的细微间隙(如 5G 毫米波连接器的超薄绝缘层)。
- 模压成型:固态硅胶需人工预成型,加压时流动方向随机,易导致局部厚度偏差(如某汽车连接器模压产品厚度公差达 ±0.05mm,而注射成型可控制在 ±0.01mm)。
-
五金嵌件精确定位
- 注射成型:模具内置精密定位销(如 MISUMI 定位衬套,公差 ±0.002mm),配合机器人自动插嵌件,确保铜端子等五金件偏移 < 0.01mm。例如泰科电子的高速连接器,通过 LIM 工艺实现 100pin 端子的同心度误差 < 5μm。
- 模压成型:人工放置嵌件易产生位置偏差(±0.03mm 以上),且硫化压力(5 - 10MPa)可能导致嵌件移位,无法满足高频信号传输对结构对称性的要求。
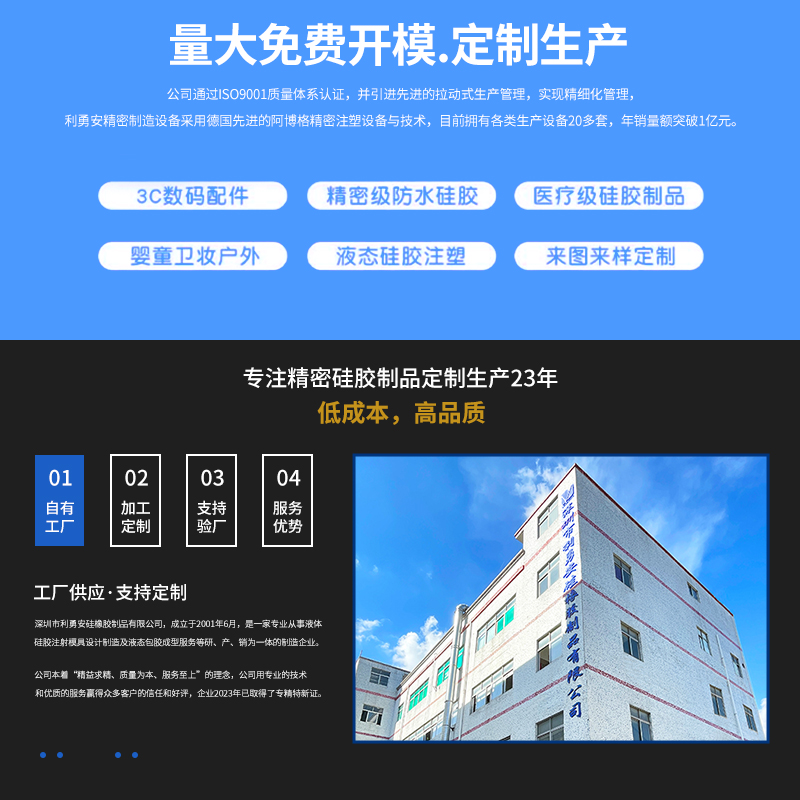
-
界面结合强度
- 注射成型:LSR 与金属 / 塑料通过化学交联(如使用道康宁 1200 底涂剂)形成化学键合,剪切强度 > 5MPa,可承受 1000 次热循环(-40℃至 120℃)无脱胶。例如医疗内窥镜连接器,需在 2MPa 水压下保持 100 小时不渗漏。
- 模压成型:物理嵌合方式(如过盈配合)在高温或振动环境下易失效,某汽车传感器模压密封件在 10 万次振动测试后出现 15% 的泄漏率,而注射成型产品泄漏率 < 0.1%。
-
薄壁结构成型
- 注射成型:可成型 0.2mm 壁厚的密封唇(如某微型防水连接器),LSR 的低粘度确保薄壁处填充饱满且无气泡。
- 模压成型:壁厚 < 0.5mm 时易出现缺料、分层,需增加壁厚至 0.8mm 以上,导致连接器体积增大,不符合小型化趋势。
-
自动化与一致性
- 注射成型:全自动化生产(如住友电动注塑机 Cycle Time≤15 秒),单模腔日产量可达 1.2 万件,CPK 值稳定在 1.67 以上(不良率 < 0.0003%)。某 5G 基站连接器项目,LIM 工艺比模压节省 70% 人力成本。
- 模压成型:人工放料、取件效率低(Cycle Time≥2 分钟),且每模需修剪飞边,导致尺寸波动(如某 HDMI 接口模压产品同心度 CPK 仅 0.8,需 100% 全检)。
-
材料利用率
- 注射成型:热流道无废料,材料利用率 > 99%,对于医疗级铂金硫化硅胶(成本约 300 元 /kg),单件材料成本可降低 40%。
- 模压成型:流道废料率达 20%,且飞边修剪产生二次废料,某精密连接器项目统计显示,模压工艺每年多消耗硅胶原料 15 吨。
- 医疗领域
- 美敦力植入式心脏起搏器连接器:通过 LIM 工艺实现钛合金外壳与硅胶的无缝结合,耐人体体液腐蚀 20 年以上,尺寸公差 ±0.005mm。
- 汽车电子
- 特斯拉 Model 3 高压连接器:采用恩格尔 e-motion 注塑机注射成型,耐 1000V DC 电压,通过 - 40℃至 150℃热循环测试 1000 次无老化,满足 ISO 6469 电动汽车安全标准。
- 通信领域
- 华为 5G 基站天线连接器:注射成型的 PTFE 包胶结构,插损≤0.2dB,回损≥25dB,在 100GHz 高频下信号传输稳定。
- 硫化温度不均:模压模具通过热板传导加热(温差 ±5℃),导致硅胶交联程度不一致,某精密连接器模压产品不同部位硬度差达 ±5 邵氏 A,而注射成型硬度波动≤±1 邵氏 A。
- 压力分布差异:模压的面压力(5 - 10MPa)远低于注射的点压力(20 - 50MPa),无法压实细微结构,如 0.3mm 间距的多针脚连接器,模压易出现针脚间硅胶填充不足,导致绝缘失效。
高精度连接器的性能要求(如信号完整性、防水可靠性、微型化)与规?;枨?,决定了其必须依赖注射成型的精密温控、高压注射、化学结合三大核心优势。模压工艺在精度、效率、一致性上的先天不足,使其仅能用于普通消费级连接器(如手机耳机插孔),而在汽车、医疗、通信等高端领域被注射成型全面取代。
深圳市利勇安硅橡胶制品有限公司—专注液态硅胶制品精密技术研发24年,联系电话:134-2097-4883。